I bought a Shrinker Stretcher machine. I have seen them used on some Youtube channels and they looked pretty handy. They seem to help a lot in making tighter curves and radiuses. The English Wheel is handy also, but the Shrinker Stretcher seems to speed up some operations a lot. Also – at my skill level – shrinking edges with just a hammer and a dolly (or stump) is challenging. Making an even shrink along an edge is especially difficult. So, I decided to try it out.
How a Shrinker Stretcher works
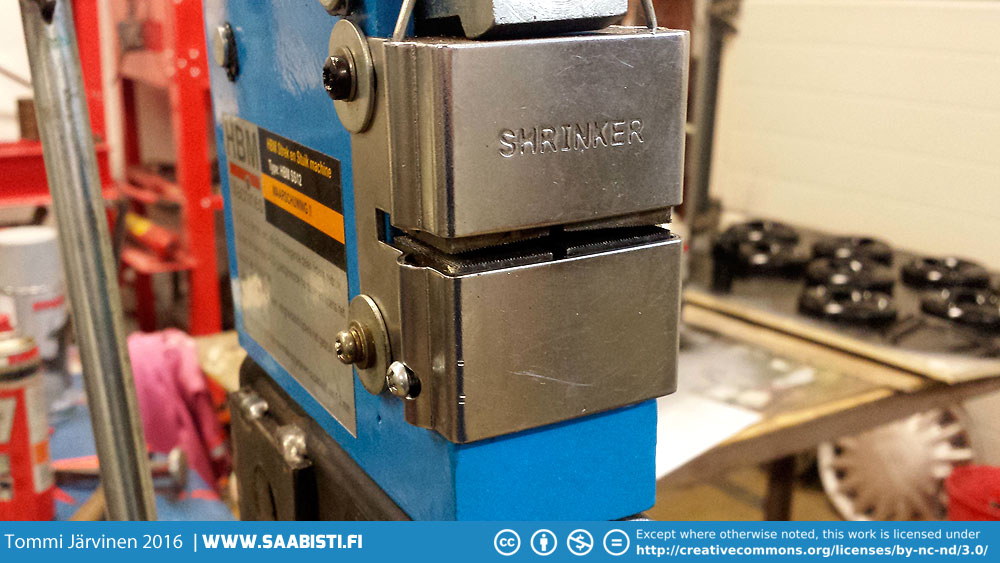
The device comes with two sets of jaws. One set for shrinking and another for stretching. The jaws clamp on the piece of sheet metal and pull the metal in towards the center (or push out if stretching) when you pull on the handle. This forces the metal to curve.
The jaws can shrink and stretch steel about two inches or 5 cm deep, and around 1 mm thick.
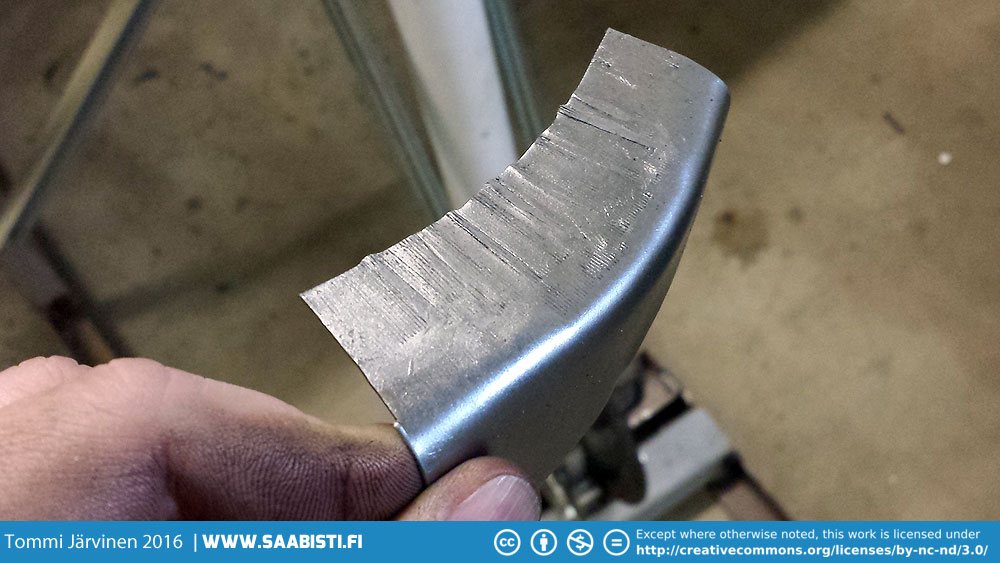
Above you can see the teeth marks the jaws make on the metal. These need some smoothing out after the desired shape has been attained. An English Wheel is a great help.
Foot operation stand
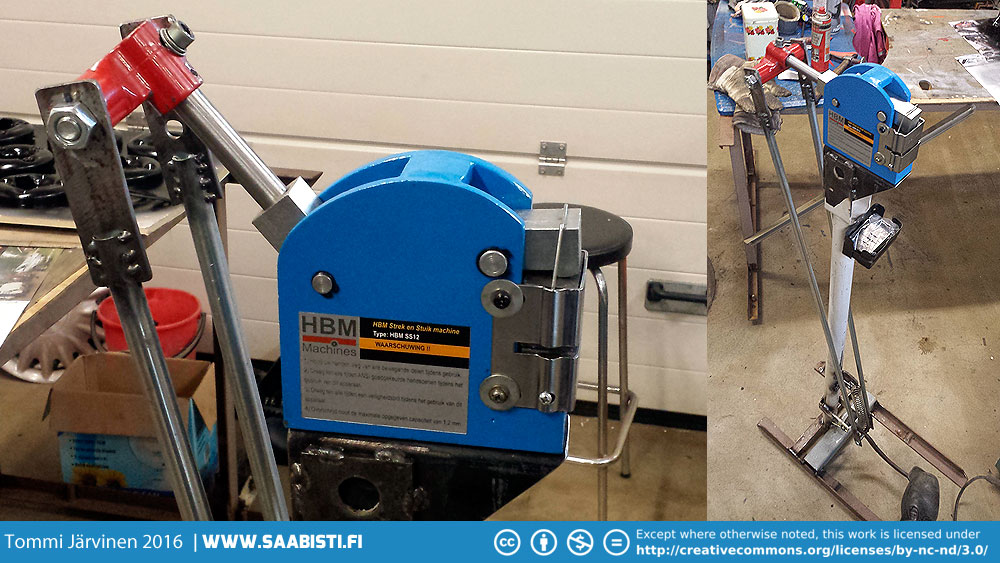
Already after my limited experience I would say that a foot operation stand is a must. A stand would have cost almost as much as the device, so we decided to make one of scrap metal. The pedal is a Saab 96 brake pedal.
The foot stand gives you a lot more power but it also frees up both hands to hold and guide the piece you are working with.
Repairing a Saab 99 Turbo rear brake dust shield
So here’s the first real test repair where I used the shrinker stretcher.
All in all I have to say that using the shrinker was a lot easier than I thought. Ofcourse making complex panels is a completely different thing, but for small parts like this it seems a real helper.