It is becoming increasingly difficult to find new directional light lenses for the two-stroke bullnose Saabs. Or actually it seems almost impossible. And I need four of them for the Saab Sport – and a few spares wouldn’t hurt.
I have a few lenses that are in more or less decent shape, so I figured I could try and make copies of them. I read about polyester resin casting using a silicone mold, and decided to give it a try. This is a pretty popular way to make hobbyist plastic parts for model railways or scratch built scale models, so i figured it can’t be too difficult.
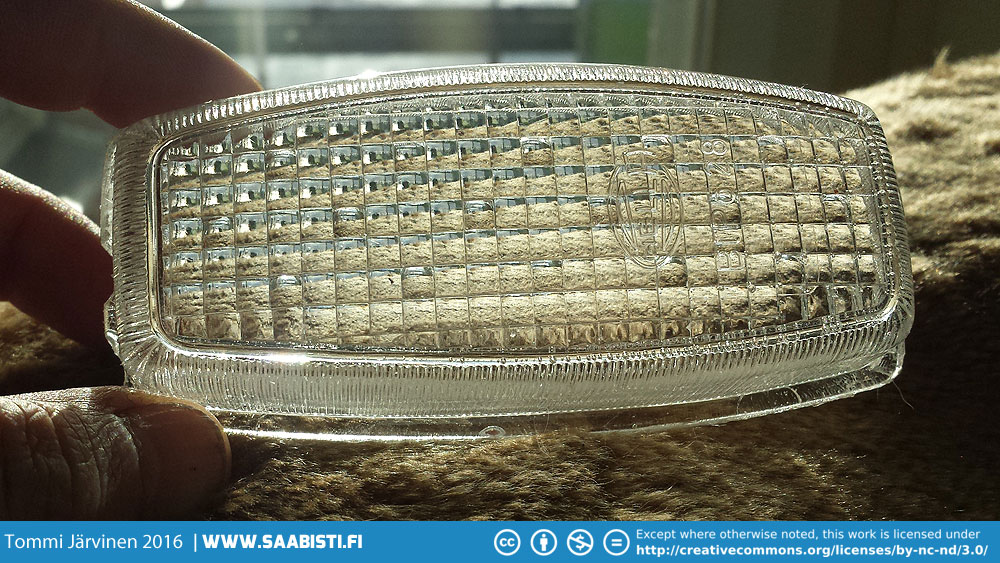
I was actually somewhat surprised, but making a polyester resin casting worked out very well as you can see above. Basically what you do, is make a two-part mold (it needs to open up to remove the finished piece) out of silicone mold rubber. The mold rubbers available come in many flavors – soft, hard, heat resistant, not heat resistant, etc. Then you pour in polyester casting resin and wait for it to cure and harden. After it has cured you open up the mold, take out the part and remove any overflow or excess resin. You can buy suitable materials in most hobbyist stores or online.
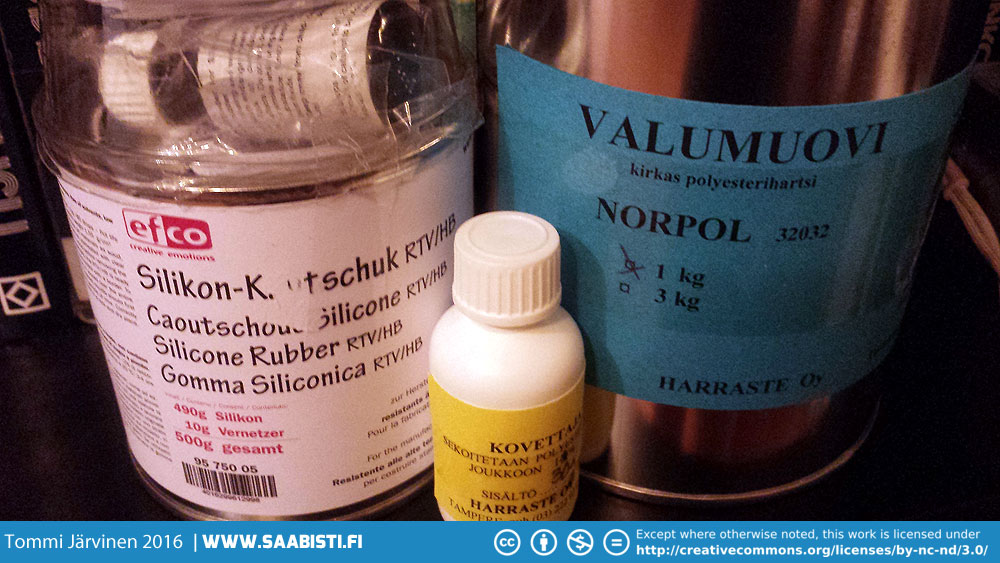
As I have not done any of this before I used what the local hobby store had (Harraste, Tampere). Efco Silicone mold rubber and Efco Polyester casting resin. Efco Polyester resin is water clear and should make very nice clear plastic parts. There are a few drawbacks – polyester resin is hazardous to your health when casting and it does shrink a bit when curing ( 6 to 8 %). So you will end up with a slightly smaller part than the original.
UPDATE: I have been recommended UV protected polyurethane instead of polyester. It is more impact resistant and should not yellow over time. I tested the polyester lens and it does break quite easily. I will try out polyurethane and report on the results.
Both – the silicone rubber and the casting resin – are two component chemicals, so they are mixed in a very specific ratios with the accelerator. There is no hurry in the mixing as the working time is usually at least 15 minutes before they start hardening. Read the instructions.
Making a silicone rubber mold
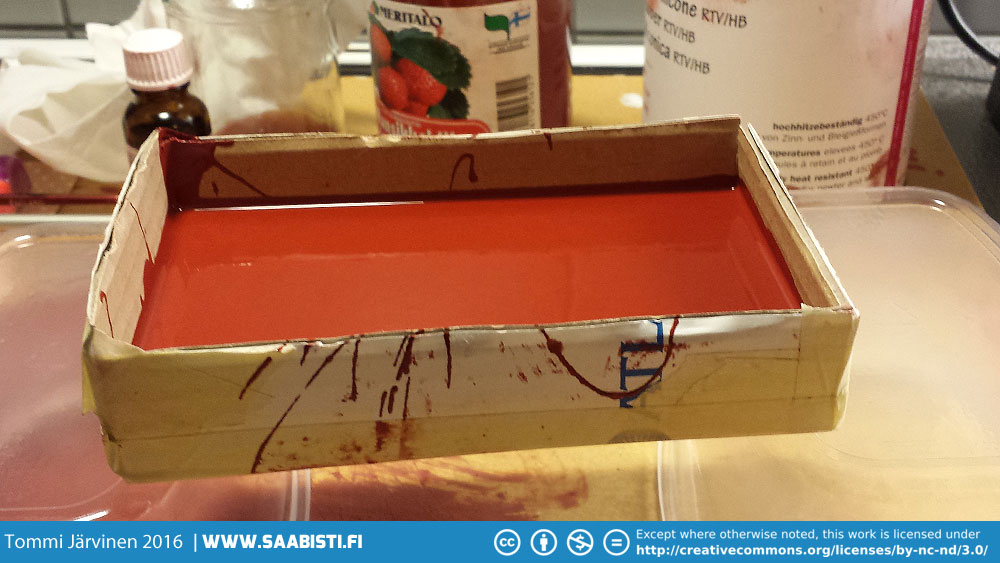
First I cast one half of the mold. The inner part of the light lens. You need to make a little tub for the part and design it so that the silicone rubber doesn’t get too much under the part. Otherwise it is hard to remove the original from inside the silicone.
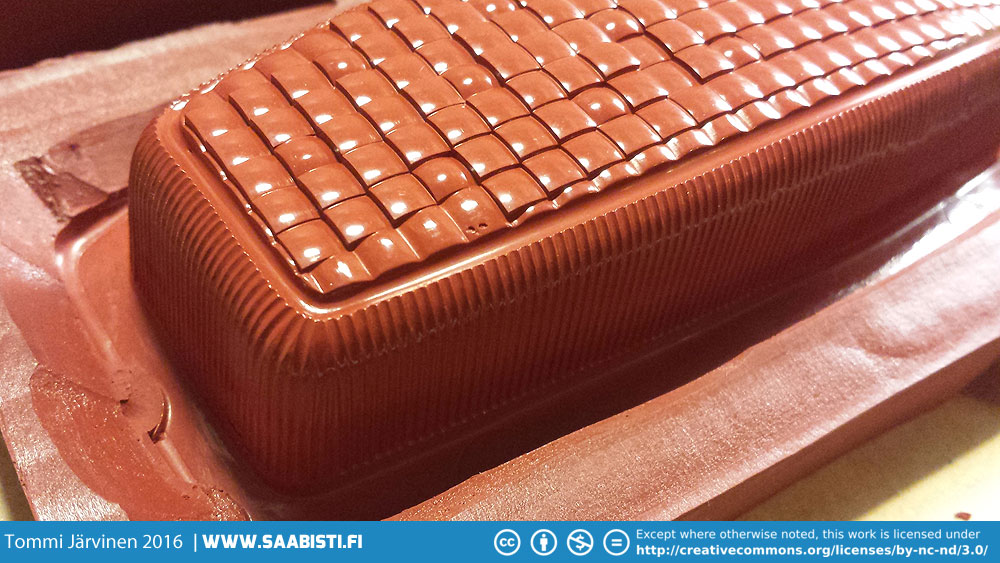
As you can see from the photo above the silicone reproduces all the surface detail of the original piece. Including all the scratches and other imperfections.
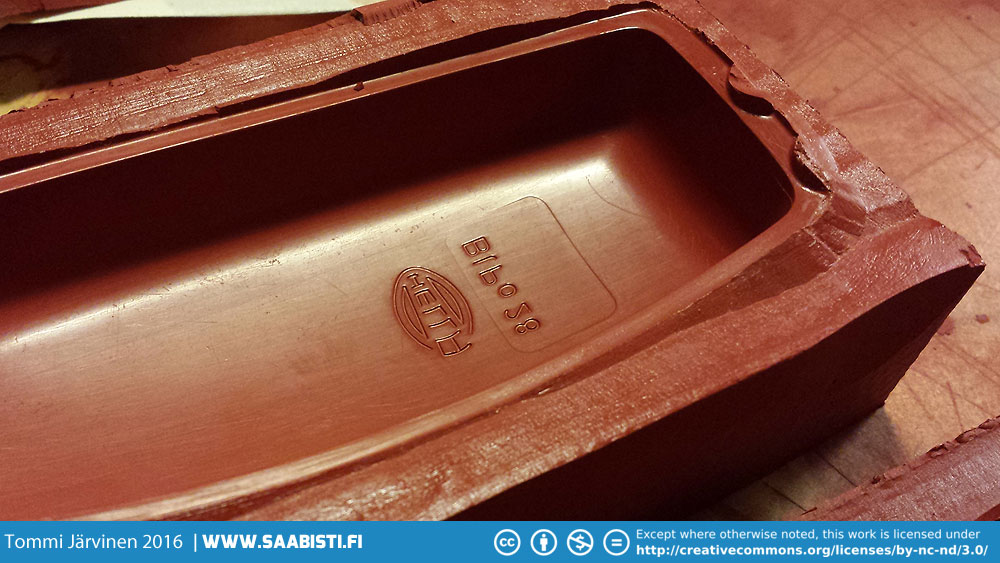
When the first half was done I applied some mold release (Vaseline grease) on the edges of the first half. I then put the original light lens back in the mold and made a new tub for it, proceeding to cast a new layer of silicone rubber on top.
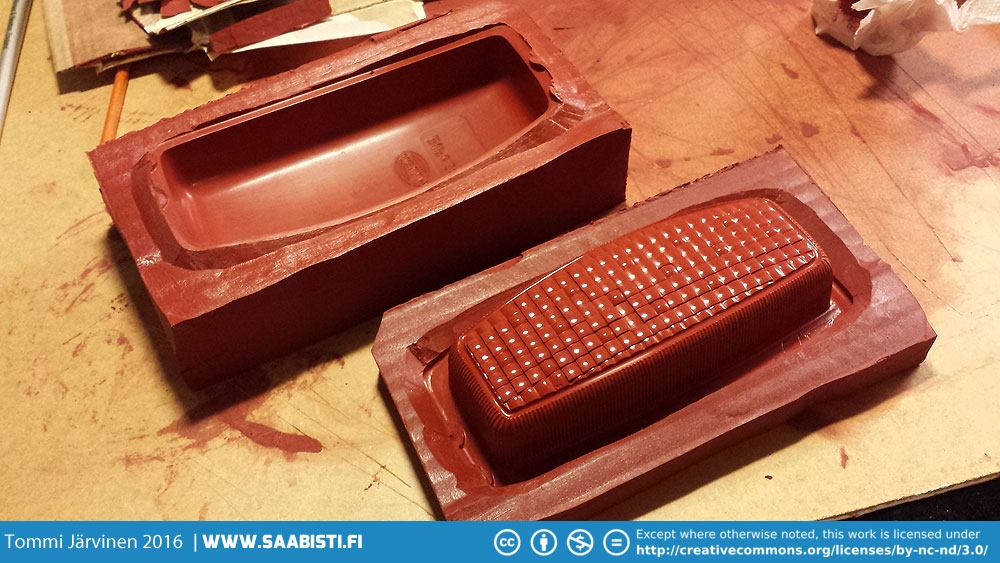
Polyester resin casting
Next I cut a few holes at the highest point of both ends of the “lid”, so I can pour in the polyester resin. The second hole is for the air to escape as the resin displaces it. You know that the mold is full when the resin comes out of the second hole.
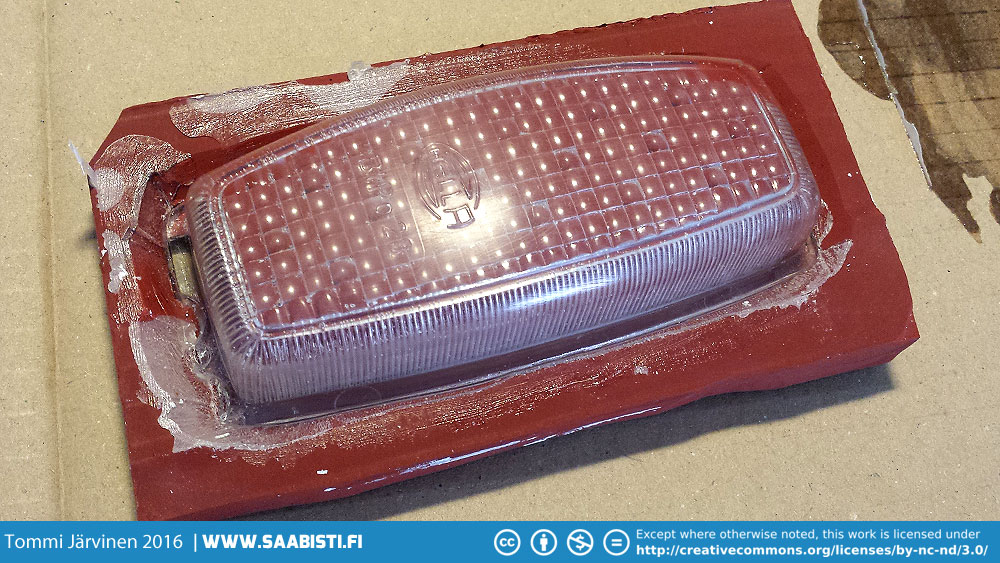
Above you can see the cast part still attached to the mold half. On the left you can see the small square hole where the resin was poured in. There is a similar hole on the other end. The holes need to be at the highest point so you will not end up with a partially filled mold.
As the silicone is quite stiff and the polyester resin shrinks a little when curing it can be quite tricky to remove it from the mold. Despite being careful I tore the mold a little. Nothing to prevent using it, but I need to be more careful with it.
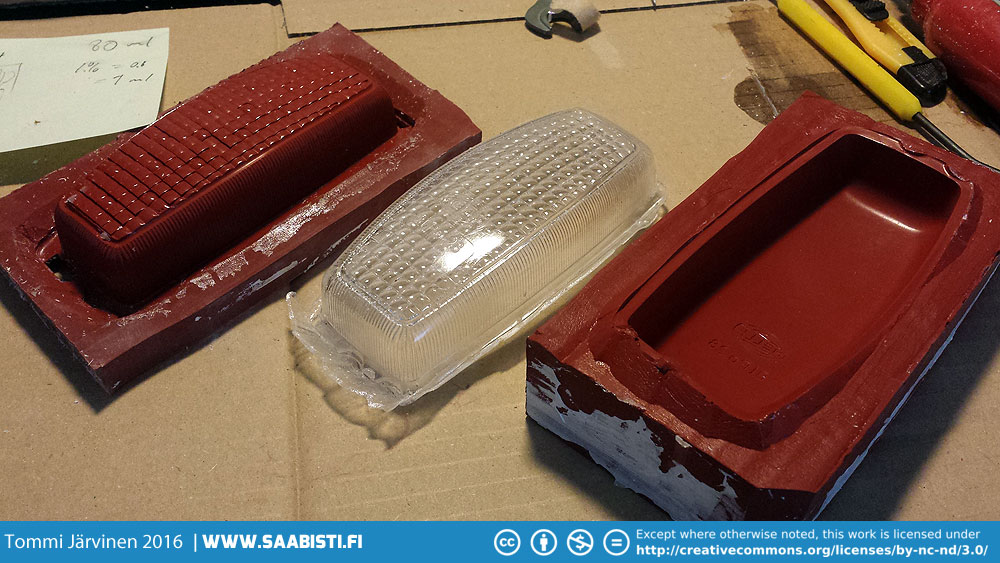
Above you can see both the mold halves and resin part just removed from the mold. Some cleanup required.
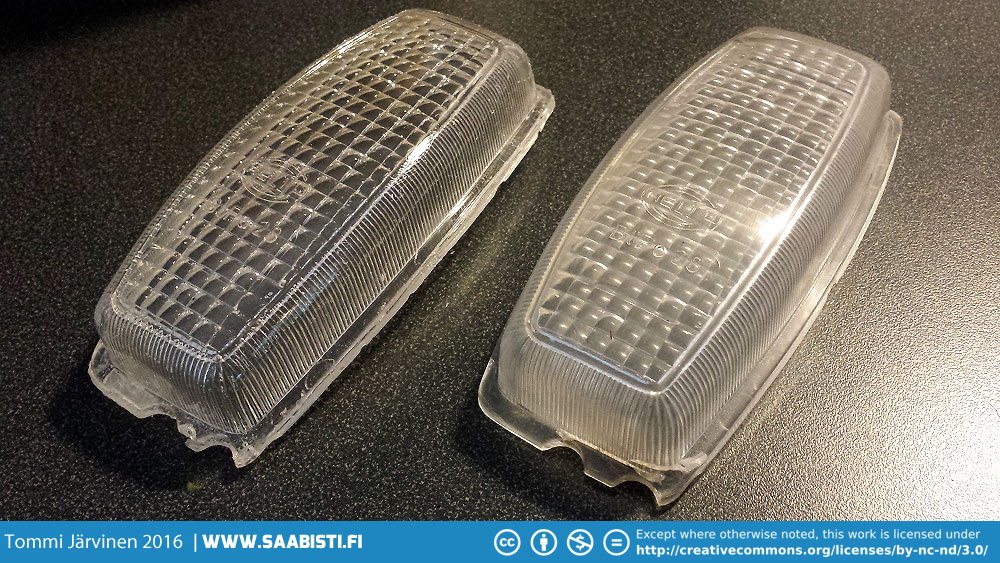
New polyester resin light lens for the Saab Sport on the left and a Saab original on the right. So far looking great.
There is one more downside to polyester resin. Most of them yellow over time if not UV protected. You can coat the piece with UV protecting agent though. Some of the resins also contain UV protection chemicals.
I don’t know how good the Efco resin is in this respect so I’m going to test the part in my two stroke. I’ll install one polyester lens on the car and store another in dark cool place for the same period and see if there is a difference.
Also I don’t know if the resin can withstand all the weather – rain, sun, stones etc. as well as the original. But I think after the summer I will pretty much know if polyester lenses are a go for the Saab Sport.
Please let me know if you have experience in polyester resin casting parts and know suitable resins with good UV properties.
Nice job Tommi, and the new lens has greater transparency too! Should you need any additional molding tips don’t hesitate to ask I have 30+ years experience there…
Hi Gerald,
Thanks for the offer – I’ll be sure to ask you if there’s need to do something more complicated than a simple two part mold.
I already got some tips elsewhere. Mainly that a better option for the casting material would be UV-protected polyurethane. It should be more impact resistant and it should not yellow over time. I’m going to buy a batch of that too and test it.
Br, Tommi
Good going. UV protection is certainly a must. You might check out a product called Lucite which artists have used in the making of sculptures. Your mould looked terrific btw! Did you pre-paint the surface or put it in a vacuum chamber? ..those are several steps to prevent air entrapment. Someone might start a small business by re-manufacturing some of the old Saab parts. Any idea if the original molds for older Saabs still exist?
Thanks, I will check it out. Another product that was recommended to me was Crystal Clear 200 or 202 polyurethane. (Link to a Finnish shop: http://silcom.fi/fi/Polyuretaanihartsit/6/Crystal+Clear+200/31)
The polyester piece is indeed quite brittle. I did some impact testing by knocking it on the table and it chipped immediately. So I will definitely try another material.
The original lenses were made by Hella. I don’t think they have the molds and if they did the market is probably way too small for injection molding.
Hi, I´m from Portugal and i´m looking for saab 99 turn signals, can you make some or tell me were i can order. thank you.